Design-Build Construction
The design-build process allows project owners to get a new building or construction project done faster and with better results. This project delivery method reduces the number of contract negotiations, contractor markups, and project delays. Instead of hiring an architect, engineer, and general contractor as separate consultants, design-build involves a single-source who brings all the expertise needed for designing, estimating, and building the project into a single contract.
The benefits of this method include reduced costs, more efficient schedules, more reliable outcomes, and an increase in communication between parties involved in the projects. It’s a method of construction where you hire one company to design, bid, and build your new project. This means that from the very beginning there is no separation between design and construction. You don’t have to worry about hiring an architect first or worrying about getting costs marked up by contractors on top of everything else.
Pacific West has been following this process with all of our construction projects because we understand how much it benefits both our clients and customers.
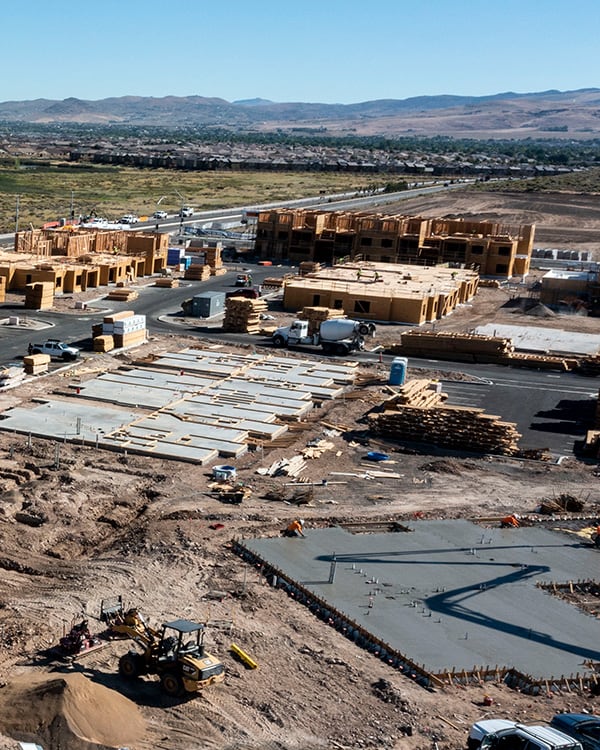
The Traditional Construction Process: Design-Bid-Build
Traditional project management requires the project owner to manage multiple separate contracts, which all-too-often creates problems between the parties.
In the event that something goes wrong or an unforeseen circumstance requires changes, there is a blame-game between the architect, engineer, and general contractor when it comes to cost overruns. Changes in schedule often lead to litigation and delays, which are costly mistakes that could be avoided by going with a design-builder.
The design-bid-build process also tends to be slower, as each stage must be completed before moving onto the next. The design-build process allows design-builders to work on multiple stages all at once.
Our Take on the Design-Build Process
We’ve restructured and repurposed the traditional design-build construction process, allowing us to significantly cut construction and project costs, and provide our project owners with a single-source they can depend on.
We apply superior design and engineering. We create products that maximize the use of off-site manufacturing and modular construction. We use products that incorporate familiar assemblies and building processes. It’s a familiarity that exponentially increases efficiency.
Because we use a repeatable and scalable system we can establish a historical standard, a baseline. That allows us to accurately estimate material and construction costs before construction begins. In fact, we’re so confident of our estimates that we guarantee them.
We also self-perform most trades, from framing to painting. This provides us with exceptional control over a building’s structure. It also streamlines scheduling, assists with risk management, and improves quality control.
To avoid price fluctuations and supply chain issues, we purchase many materials in bulk direct from the manufacturer.
We also employ our self-designed customized technology, a $4.5 million investment that ties everyone together and keeps everyone on the same page.
All told, it’s a design-build approach that allows us to greatly reduce labor and material costs. It eliminates virtually all stages of markup. It speeds up construction. It enhances quality.
It’s a better way of real estate development.
Design-Build Process Steps
1. Design-Build Team Procurement
A design-build process begins with the owner choosing a design-build team. It is common for owners to vet potential candidates thoroughly, selecting the contractor-architect team with the most design-build experience and which best understands the company’s vision, needs, and budget.
Despite being an important factor, cost should not be the only factor influencing the final decision. Owners may be tempted to choose the lowest price, but a smart owner understands the value of hiring a qualified design-builder, and chooses primarily based on the design-builder’s expertise.
Once a design-builder is chosen, a design-build contract is written and agreed upon.
2. Pre-Construction
Before design and construction can begin, architects, engineers, contractors, and other consultants all work together to assess structures, electrical systems, and other aspects of the project. These assessments allow for a thorough assessment of the construction site, which helps the design-build team to maximize efficiency throughout the project. Once this step is complete, they create preliminary drawings for approval by the project manager.
3. Design
Once the preliminary drawings are approved, the design phase begins. Next, the architect will complete the final drawings for the project after he or she obtains approval from the client. Because the architect has been working with all other parties closely, drawings will be more accurate and will reduce the risk of construction problems and change orders down the road.
4. Build
It is common for design-build projects to have some overlap between the design and construction phases, which may significantly speed up the process. If the design-build team has not already started initial construction work during the design phase, it can get started immediately afterwards. Design-build projects have just one point of contact throughout the construction process, which simplifies communication. Because all workers are on the same team, striving for the same goals and milestones, and therefore any problems or issues are commonly handled quickly and efficiently, accountability is established and changed orders are rare or nonexistent. Because of the collaborative nature of the design-build delivery method, change orders are usually minimal and, in some cases, non-existent.
Pacific West Companies uses the same subcontractors, the same architects and engineers, the same materials, and the same suppliers — all of whom specialize in multi-family building — we are able to use the same design assemblies job after job after job. This familiarity with the process is the most proven method to eliminating mistakes.
5. Post-Build
The design-build team provides an overview of the project deliverables upon completion of the project, including instructional videos, documented procedures, and in-person training sessions for applicable personnel. Because all of the work is done by a single entity, the post-construction process is often much more streamlined than when designers and contractors are working separately.
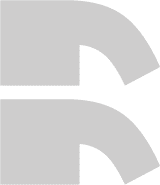
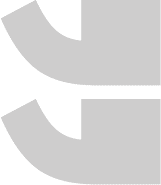
We’ve been very impressed with Pacific West’s design-build process. It definitely increases construction efficiency and quality.
